…and is it left too late and takes too long?
Well, the short answer is that “everyone” in your organisation is responsible for the safety of the product. But in reality, it will typically be delegated to an individual from the Engineering team or the Safety, Quality or Reliability teams.
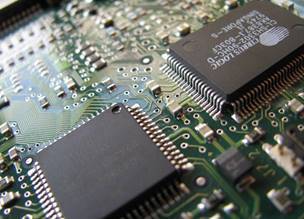
Which standards…which tasks?
Standards such as ISO26262, IEC61508, ARP4761, MIL-STD-882E and ISO21434, among others, require you to perform numerous safety tasks – to prove that your design is safe.
These tasks typically involve a wide range of studies, including:
- HAZOP
- HARA
- SIL or ASIL
- FMEA
- FTA
- Reliability analysis
- FMECA
- FMEDA
- FMES
All of these tasks aim to demonstrate that the design meets or exceeds your customer’s safety targets. These safety tasks require extensive documentation to evidence your analysis.
What history has told us…
The biggest mistake we often see is that it is not until the product is reasonably well down the road of its design life cycle, maybe even at the prototype stage, before the safety flag is raised. Consequently, there’s a last-minute rush to retro-fit the quality, reliability and safety analysis. The safety-delegated individual then has the daunting task of assembling all the information and results into a coherent System Safety Analysis or Safety Case at short notice.
Why does it take so long?
We all know that time is money, and bringing all these individual but related analyses together can take considerable time to do well.
Furthermore, design iterations as the product evolves are a fact of life. But making the design changes means more work on the documentation. All of the safety analyses need to be updated to reflect the “new” current status, including changing the figures, re-visiting some or all of the workshops and updating the FMEAs and FTAs, together with other individual analyses, before finally recompiling the Safety Case. This is likely to consume much more valuable time of those delegated.
Some friendly advice
If this sounds all too familiar, then there are two things you should consider doing:
- First, start the safety analysis tasks earlier if possible and consider sharing the burden. If you find you have a shortage of in-house skills, or are running out of time, safety consultants like Wilde can support you through the processes.
- Second, use facilitating software like Medini Analyze from Ansys – an integrated tool that guides you through the requirements of the Standards and conveniently incorporates all the tasks within a single environment. Medini has a highly customisable and automatic documentation generation capability, which makes incremental changes and updating both quick and reliable, while also ensuring invaluable end-to-end traceability.
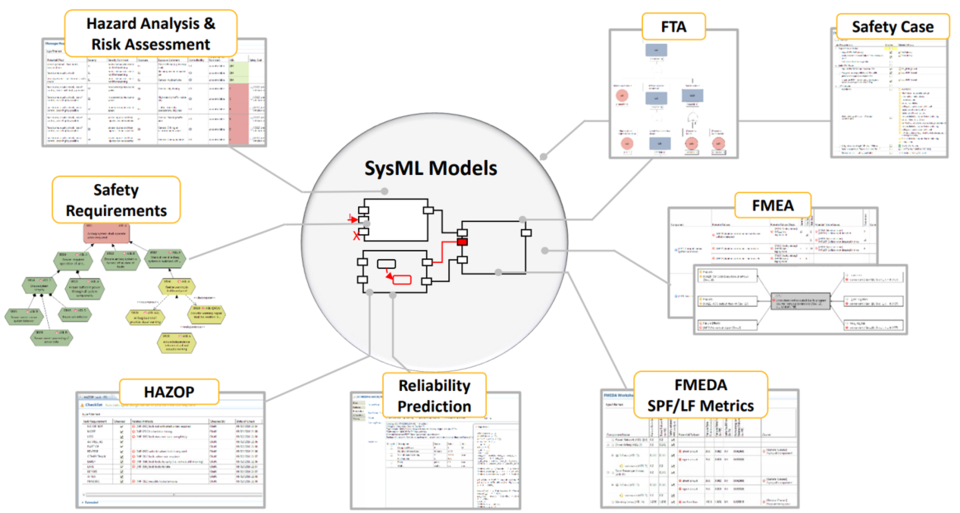
How we can help
I hope this article has been useful, please contact us at Info@wilderisk.co.uk to discuss how we can help. For more information on Medini Analyze, visit https://wilderisk.co.uk/medini